Key Takeaways
- SQEP Compliance Matters: The Walmart SQEP program aims to improve the quality of inbound shipments through strict packaging, labeling, and PO (Purchase Order) accuracy requirements. Suppliers need to stay vigilant to avoid deductions.
- Disputing Deductions is Possible: Many SQEP-related charges are not valid and can be disputed with the right documentation and approach. Understanding common defects in the program is key to identifying disputes.
- Improving Compliance: By understanding the different phases of SQEP and common defect categories, suppliers can improve their compliance and reduce future deductions, ultimately protecting their margins.
What is SQEP and Why Was It Created?
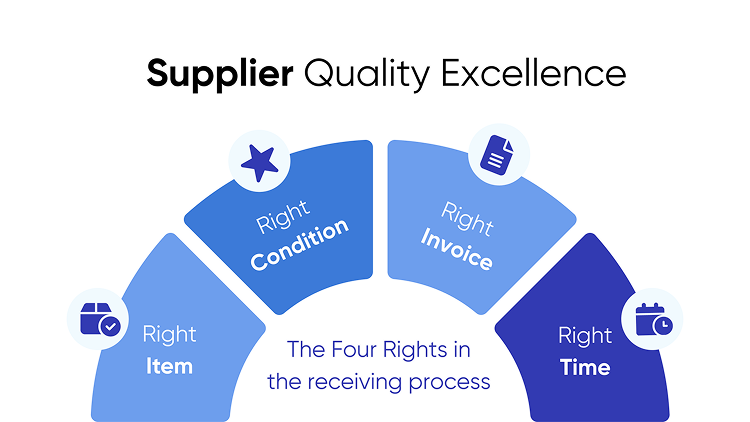
Walmart’s Supplier Quality Excellence Program (SQEP) was launched to improve inbound quality throughout Walmart’s US Supply Chain. The initiative focuses on achieving best-in-class status through defect elimination, value-added services, and a zero-based mindset.
The program evaluates, measures, and monitors suppliers’ inbound quality with several key objectives:
- Exceeding customer satisfaction
- Improving end-to-end accuracy and visibility
- Driving continuous improvement toward perfection
- Implementing First Time Quality (FTQ)
- Reducing operational costs
SQEP applies across all Walmart U.S. distribution networks, including regional Distribution Centers (DCs), ecommerce Fulfillment Centers, and specialized facilities. The program centers on delivering the “four rights” in the receiving process:
- Right item
- Right condition
- Right invoice
- Right time
Understanding the Four Phases of Walmart SQEP
Walmart SQEP was implemented in multiple phases, each targeting different aspects of the supply chain. Understanding these phases is critical for suppliers who want to maintain compliance and avoid unnecessary charges.
1. PO Accuracy & ASN Issues
Phase 1 focuses on purchase order accuracy and Advanced Shipping Notice (ASN) compliance issues. Common defects in this phase include:
- Overages: Shipping more than the ordered quantity
- Canceled PO/Line: Shipping against canceled purchase orders or line items
- Wrong Item/Pack: Items that don’t match the PO or incorrect vendor pack quantities
- ASN Issues: Missing ASNs, late ASNs, or ASNs with errors
- No ASN Label: For DSDC (Direct Store Delivery Consolidation) shipments missing required ASN labels
These issues directly impact Walmart’s ability to receive and process your shipments efficiently, leading to additional handling costs that may be passed back to suppliers.
2. Barcode & Labeling Compliance
Phase 2 addresses barcode and labeling requirements, with defects broadly categorized as:
- Barcode Compliance: Wrong format, incorrect quantity (not on two sides), missing barcodes, or GTIN (Global Trade Item Number) mismatches with item setup
- Label Compliance: Missing or incorrect information, such as product descriptions, dates, or required markings
- Hazmat Compliance: Missing or covered hazardous materials labels
Some specific examples include:
- Wrong barcode format (not in an approved format)
- Barcodes not present on at least two sides of the case
- Missing item descriptions on cases
- Missing required product dates
- Missing or incorrect STOP labels for master packs
3. Pallet, Packaging & Load Quality
Phase 3 focuses on the physical integrity of shipments, including:
- Packaging Compliance: Weak packaging, poor perforations, missing trays, loose wrapping, improperly sized cases
- Pallet Labeling: Missing shipping labels or incorrect pallet markings
- Pallet Securement: Poor wrapping, missing trays for bagged items
- Pallet Build: Overhang, excessive height, incorrect tier stacking
- Pallet Quality: Non-compliant pallets or wrong pallet size
- Load Stability: Shifted or unstable loads, non-palletized freight
- Load Segregation: Improper separation of different PO types or inefficient grouping of items
Each of these issues can cause delays, damage, or inefficiencies in Walmart’s distribution network, generating additional costs.
4. Scheduling and Transportation
This phase is still under development, with timing listed as “TBD” in the current documentation. It will likely focus on transportation compliance, appointment scheduling, and related logistics issues.
Walmart SQEP Audit Checklist
Use our interactive SQEP Audit Checklist below to assess your compliance with Walmart’s Supplier Quality Excellence Program (SQEP). This tool will guide you through each phase of the process and help you track potential compliance issues.
Overall Audit Progress
Section Completion
Section 1: PO Accuracy – 0%
Section 2: Barcode & Labeling – 0%
Section 3: Packaging, Pallet, Load Quality – 0%
Section 4: Specialized Requirements – 0%
Non-Compliance Issues Log
Document any non-compliance issues identified during the audit below.
Category | Specific Issue | Action Required | Owner | Due Date | Actions |
---|
Root Cause Analysis
Identify primary causes of non-compliance issues:
Shipment Approval
Follow-Up Actions / Notes
Audit Information
Share audit report with your team.
How to Use This Tool
- Personnel: Assign dedicated QA staff to perform the audit.
- Documentation: Record all findings and corrective actions in the Summary tab.
- Follow-up: Address all non-compliance issues before shipping.
- Continuous Improvement: Update your internal processes based on audit findings.
- Navigation: Use the tabs above to switch between the Audit Checklist, Summary, and Help sections. Click section headers in the Audit Checklist to expand/collapse them.
Key Walmart Contacts
- SQEP Contact: [email protected]
- Package Testing: [email protected]
- Labeling Compliance: [email protected]
Resource Links (Check Retail Link for Updates)
- Walmart Secondary Packaging Standards
- Transit Testing Information
- SQEP Program Overview
- SQEP Web Portal (via Retail Link)
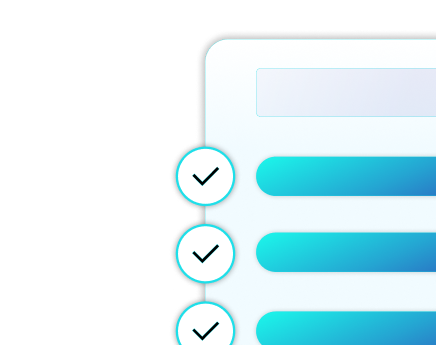
What Charges Can You Expect?
SQEP defects can lead to various charges, commonly referred to as “FixIt” defects. These are categorized into specific sub-defects with detailed definitions:
Barcode Compliance Charges:
- Wrong format barcodes
- Barcodes not on two sides
- Missing barcodes
- GTIN mismatches with item setup
General Case Marking Compliance Charges:
- Markings not on two sides
- Missing item descriptions
- Missing required product dates
- Incorrect or missing STOP labels
Hazmat Compliance Charges:
- Missing or covered hazmat markings
- Missing or covered lithium-ion markings
- Missing or covered limited quantity markings
Packaging Compliance Charges:
- Missing bottom trays or lids
- Loose wrapping
- Poor perforations
- Insufficient packaging for fragile items
- Unsecured selling units
- Loose or metal straps
- Weak packaging or insufficient glue/tape
- Oversized or bulging cases
Pallet-Related Charges:
- Missing or incorrect mixed date labeling
- Poor securement
- Bagged items missing pallet barriers
- Pallet overhang
- Exceeding maximum pallet height
- Incorrect tier construction
- Poor quality pallets
- Non-compliant pallet sizes
Load-Related Charges:
- Shifted or unstable loads
- Non-palletized freight
- Improper PO separation
- Poor item grouping by layer
- Same items spread across multiple pallets
These charges often relate to seemingly minor issues that can create significant inefficiencies in Walmart’s highly automated distribution environment. For suppliers, even small technical violations can add up to substantial deductions over time.
The financial impact of poor Walmart SQEP compliance can be substantial. Every charge directly affects your profit margins, and the administrative burden of managing these deductions can strain internal resources. Consider the following impacts:
- Even small per-case charges can add up to thousands of dollars monthly for high-volume suppliers
- Technical violations (like barcode placement or pallet overhang) can occur across numerous shipments before being identified
- Internal teams often lack the specialized knowledge to identify invalid charges
- The dispute process requires detailed documentation and specific knowledge of Walmart’s standards
- The time and resources needed to manually track and dispute charges often exceed the value of individual deductions
This creates a situation where many suppliers simply accept these charges as a cost of doing business with Walmart, unnecessarily eroding their margins.
Can You Dispute SQEP Charges?
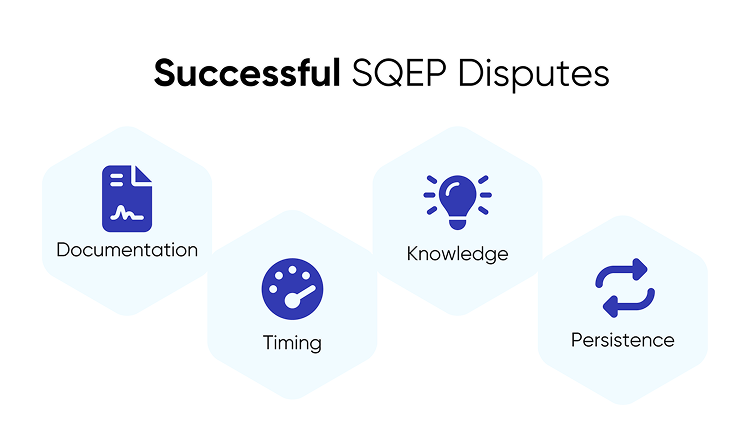
Yes. Many SQEP charges are invalid. Successful disputes require:
- Documentation: Detailed records of your shipments, including photos, ASNs, and conformity to published standards
- Timing: Disputes must be submitted within the allowable timeframe
- Knowledge: Understanding the specific standards that apply to your product category
- Persistence: Following through on the dispute process, which can be time-consuming
The challenge for most suppliers is balancing the cost of disputing charges against the potential recovery amount. Many valid disputes go unfiled simply because suppliers lack the resources to pursue them effectively.
Start Recovering Lost Revenue
Walmart’s SQEP program presents significant compliance challenges but also offers opportunities to improve operations and protect margins. While the program’s requirements are strict, many deductions are disputable with the right approach and resources.
By understanding the SQEP phases and defect categories, suppliers can both enhance compliance and identify invalid charges. Carbon6 Revenue Recovery turns SQEP compliance from a cost center into a recovery opportunity. Purpose-built for Walmart suppliers, it’s designed to help brands not only dispute invalid SQEP-related deductions but also for shortage, pricing and return claims. With Carbon6 Revenue Recovery for Walmart you can expect:
- Identification of invalid charges going back up to 2 years
- Automated dispute filing with the appropriate documentation, freeing up internal resources
- Detailed reporting on dispute status and recovery amounts
- Improve compliance to reduce future deductions
- Zero upfront costs—we only get paid when you recover funds